MACHINING TILTED PLANES
This specific function manages the angle of the orthogonal planes of the machine. It’s possible to set up an angle for the machine planes based
on the angle of the tool. This function will align the tool perpendicularly to the plane to be machined based on the tilt angle.
Previously-programmed standard machining (pockets, drilling, milling, etc.) can be performed on the new tilted plane without changing the
values entered. Enabling this function on machines with tilting headstocks and tables will allow the angle of the planes to be modified while
keeping the tool perpendicular in the “Z” axis. |
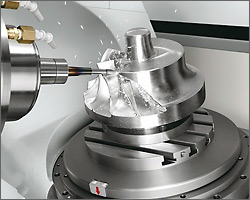 |
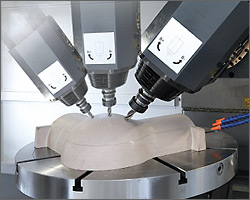 |
CONTROLLING DYNAMIC RTCP (5 axes)
The RTCP function (Rotation Tool Centre Point) is used in 5-axis machining and allows the tip of the tool to follow the programmed profile
regardless of tool orientation and length.
When the RTCP function is enabled, the CNC moves the X-Y-Z axes to keep a constant trajectory of the tool tip on the workpiece so that the tool is
always perpendicular to the profile to be machined and the workpiece evolutions or the headstock tilting are uninfluential. |
MANAGING KINEMATIC MOTION AND MACHINE CONFIGURATION
Machines with 5 axes may have different types of kinematic motions to be controlled: tilting head and rotary table, rotating-tilting table and
vertical head, rotating-tilting head, vertical head and tilting and rotary plane, in addition to the same conditions with horizontal head.
The CNC can be “set up” based on the kinematic motion of the machine, and it will automatically determine the role played by the axes.
OPTIMIZED TOOL MANAGEMENT
There may be a need during machining (especially machining requiring a lengthy period) to thoroughly manage the tools.
VSC 1040 DM can manage the duration of the tool, the maximum effort allowed, and “twin” tool changing.
The tool table includes data relative to tool duration and maximum effort allowed (in %); in addition, by providing the cutting speed data (mm/tooth).
The CNC automatically calculates the progress speed and the spindle speed to optimize removal during machining.
RESUMING SUSPENDED MACHINING
If machining is suspended due to natural or voluntary causes, it’s possible to use the one function to “freeze” the values at the time machining is
suspended, leave the execution menu, restore the tool or other, and then move close to the point where machining was suspended and resume cycle
execution, without losing the resume position and having to execute the cycle again from the first program block.
CALIBRATION AND TOUCH CYCLES
Touch can be performed on the workpieces being machined using a 3D probe in order to find the centre of circumference or flange, parallelepipeds,
angles, oblique planes, etc. The CNC has special menus dedicated to these functions.
The touch cycles can also be enabled in ISO programs and the values obtained can be used to (automatically) replace the origin points of the
programs being executed.
A special function auto-aligns the workpieces with the orthogonal plane of the machine should they not be properly oriented.
Other menus are used together with presetting to calibrate the tools (used in the tool table) and the check tool integrity cycles during program
execution.
|
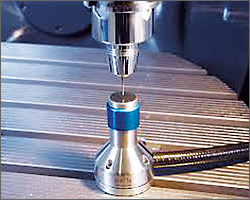 |
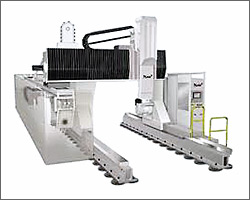 |
MANAGING GANTRY AXES
Certain machines (i.e. milling machines or portal machining centres, plotters, etc.) use 2 motors to move the same axis. The movement related to
the two motors and associated measuring systems (encoders or transducers) is to be synchronized. The CNC has this function; it allows managing
and parameterizing the two axes individually, which are then used as though they were a single axis. An alarm threshold can also be set up should
the measurement deviation between the 2 axes exceed a value introduced by a parameter. |
|